Case hardening
The process of case hardening is always used when a component is desired with a ductile core and at the same time a wear-resistant and hard surface. The workpiece made of case-hardened steel is carburized in the peripheral area and then quenched (hardened). Case hardening usually takes place at temperatures between 880 and 980 °C in an atmosphere containing carbon, so that the surface of the component is enriched with carbon by diffusion. After carburization, the component is quenched in oil, water or special polymer solutions. This results in a significant increase in hardness in the carburized region. Standard case hardening depths lie between 0.1 to 2.5 mm, but we also have workpieces with extreme case hardening depths of over 6.0 mm in our portfolio.
If nitrogen carriers (ammonia) are also added to the furnace atmosphere besides carbon, this is then called carbonitriding. Nitrogen atoms diffuse in the same way as carbon into the material surface and increase the hardness. The advantage of carbonitriding is that cheaper unalloyed steels and free-cutting and deep-drawing steels can be surface hardened.
After the hardening process, the component is tempered. Tempering is necessary to reduce tension in the component and to set the required operational strength. Case hardening at the Hanomag Heat Treatment Group is done in a gas stream or in a salt bath. In the salt bath there is the option of partial hardening without previously insulating certain regions of the workpiece. A hard and wear-resistant surface layer and a ductile core make this process the preferred heat treatment for all transmission components.
Benefits of case hardening
- Improvement of the mechanical properties
- Higher wear-resistance
- Ductile core
- Regions can be covered that are not to be hardened.
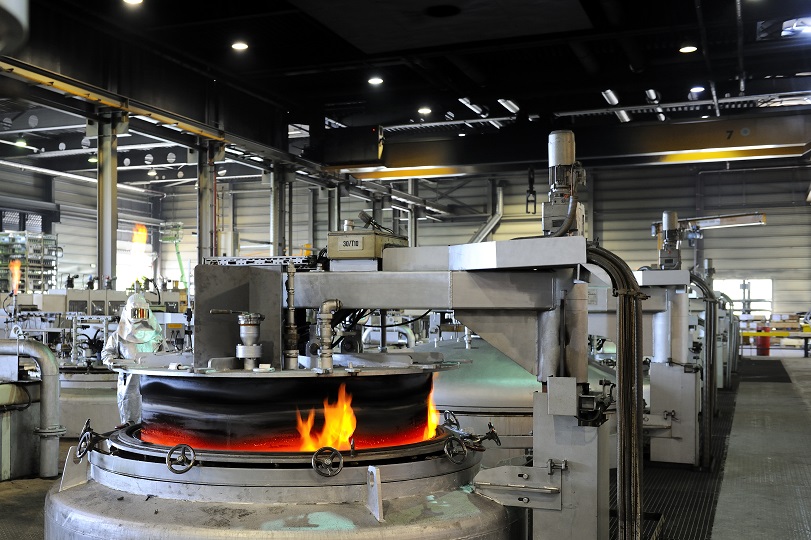