Einsatzhärten
Das Verfahren des Einsatzhärtens kommt immer dann zur Anwendung, wenn man bei einem Bauteil einen zähen Kern und gleichzeitig eine verschleißbeständige, harte Oberfläche haben möchte. Dafür wird das Werkstück aus Einsatzstahl im Randbereich aufgekohlt und anschließend abgeschreckt (gehärtet). Das Einsatzhärten erfolgt in der Regel bei Temperaturen zwischen 880 bis 980 °C in einer kohlenstoffhaltigen Atmosphäre, wodurch die Oberfläche des Bauteils durch Diffusion mit Kohlenstoff angereichert wird. Nach dem Aufkohlen wird das Bauteil in Öl, Wasser oder speziellen Polymerlösungen abgeschreckt. Infolgedessen erfährt der aufgekohlte Bereich eine deutliche Härtesteigerung. Gängige Einsatzhärtetiefen liegen bei 0,1 bis 2,5 mm, wir haben aber auch Werkstücke mit extremen Einsatzhärtetiefen von über 6,0 mm im Portfolio.
Werden der Ofenatmosphäre neben Kohlenstoff auch noch zusätzlich Stickstoffträger (Ammoniak) hinzugegeben, dann wird vom Carbonitrieren gesprochen. Die Stickstoffatome diffundieren wie der Kohlenstoff in die Werkstoffoberfläche und sorgen für eine Härtesteigerung. Der Vorteil des Carbonitrierens ist, dass auch billigere, unlegierte Stähle sowie Automaten- und Tiefziehstähle oberflächengehärtet werden können.
Nach dem Härtevorgang wird das Bauteil angelassen. Das Anlassen ist erforderlich, um die im Bauteil entstandenen Spannungen zu mindern und die geforderte Gebrauchsfestigkeit einzustellen. Einsatzhärten bei der Hanomag Lohnhärterei Gruppe erfolgt im Gasstrom oder im Salzbad. Beim Salzbad besteht die Möglichkeit der partiellen Härtung, ohne vorher bestimmte Bereiche des Werkstückes zu isolieren. Eine harte, verschleißbeständige Randschicht und ein zäher Kern machen dieses Verfahren zur bevorzugten Wärmebehandlung für alle Getriebeteile.
Vorteile des Einsatzhärtens
- Verbesserung der mechanischen Eigenschaften
- Erhöhter Verschleißwiderstand
- Zäher Kern
- Nicht zu härtende Bereiche können abgedeckt werden
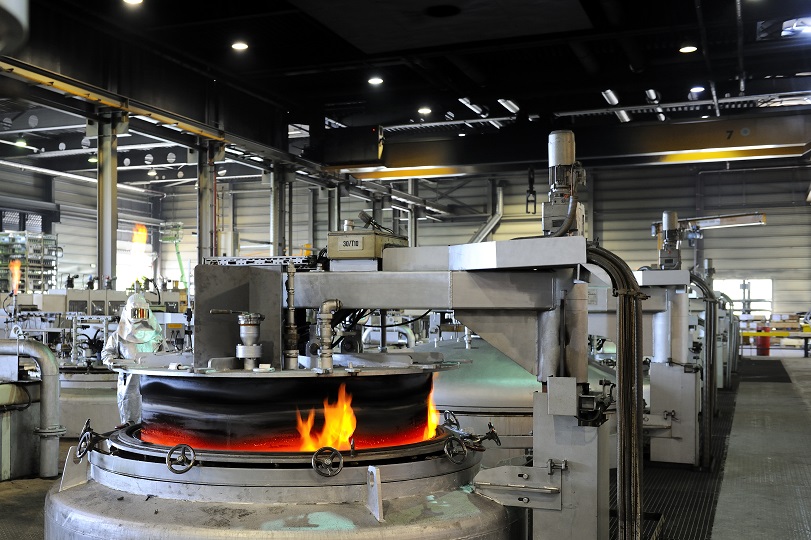