Utwardzanie dyfuzyjne
Proces utwardzania dyfuzyjnego jest wykorzystywany zawsze wtedy, gdy rdzeń elementu ma być ciągnący, a jednocześnie ma wykazywać twardą, odporną na zużycie powierzchnię. W tym celu element ze stali do nawęglania jest nawęglany w obszarze krawędzi, a następnie studzony (hartowany). Utwardzanie dyfuzyjne odbywa się z reguły przy temperaturach w zakresie od 880 do 980°C w atmosferze zawierającej węgiel, przez co powierzchnia elementu jest wzbogacana węglem wskutek dyfuzji. Po nawęglaniu element jest hartowany w oleju, w wodzie lub w specjalnych roztworach polimerowych. Wskutek tego znacznie zwiększa się twardość nawęglanego obszaru. Standardowe głębokości utwardzania dyfuzyjnego wynoszą od 0,1 do 2,5 mm, ale w naszym portfolio można znaleźć ekstremalne głębokości utwardzania dyfuzyjnego powyżej 6,0 mm.
Jeżeli do atmosfery pieca oprócz węgla zostanie dodany nośnik azotu (amoniak), proces nazywa się węgloazotowaniem. Atomy azotu podlegają dyfuzji jak węgiel do powierzchni materiału i zapewniają wzrost twardości. Zaletą węgloazotowania jest możliwość hartowania powierzchni również tańszych, niestopowych stali oraz stali automatowych i stali do głębokiego ciągnienia.
Po zakończeniu procesu hartowania następuje odpuszczanie elementu. Odpuszczanie jest wymagane w celu zmniejszenia naprężeń powstałych w elemencie i uzyskania żądanej wytrzymałości użytkowej. Utwardzanie dyfuzyjne w Grupie przedsiębiorstw Hanomag Lohnhärterei odbywa się w strumieniu gazowym lub w kąpieli solnej. W przypadku kąpieli solnej możliwe jest hartowanie częściowej bez konieczności wcześniejszego izolowania określonych obszarów obrabianego elementu. Twarda, odporna na zużycie warstwa powierzchniowa i ciągliwy rdzeń sprawiają, że ta metoda jest preferowaną metodą obróbki cieplnej dla wszystkich części przekładni.
Zalety utwardzania dyfuzyjnego
- Poprawa właściwości mechanicznych
- Większa odporność na zużycie
- Ciągliwy rdzeń
- Możliwość zakrycia obszarów nieprzeznaczonych do hartowania
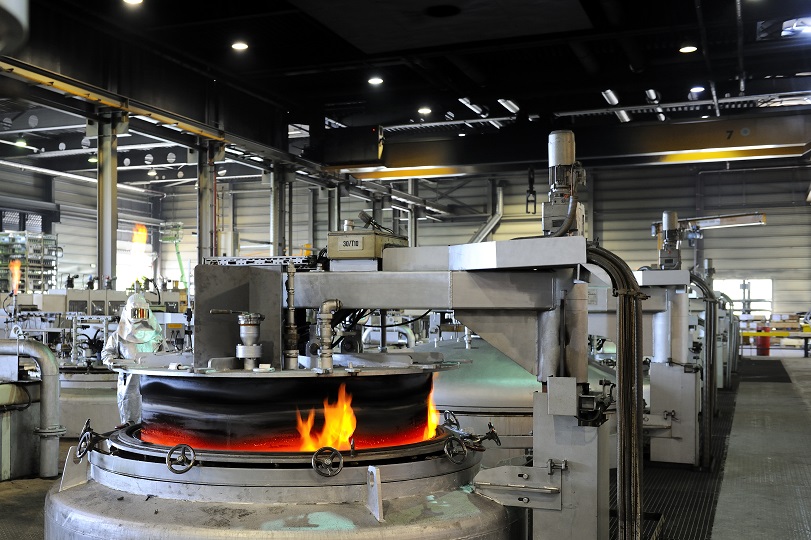